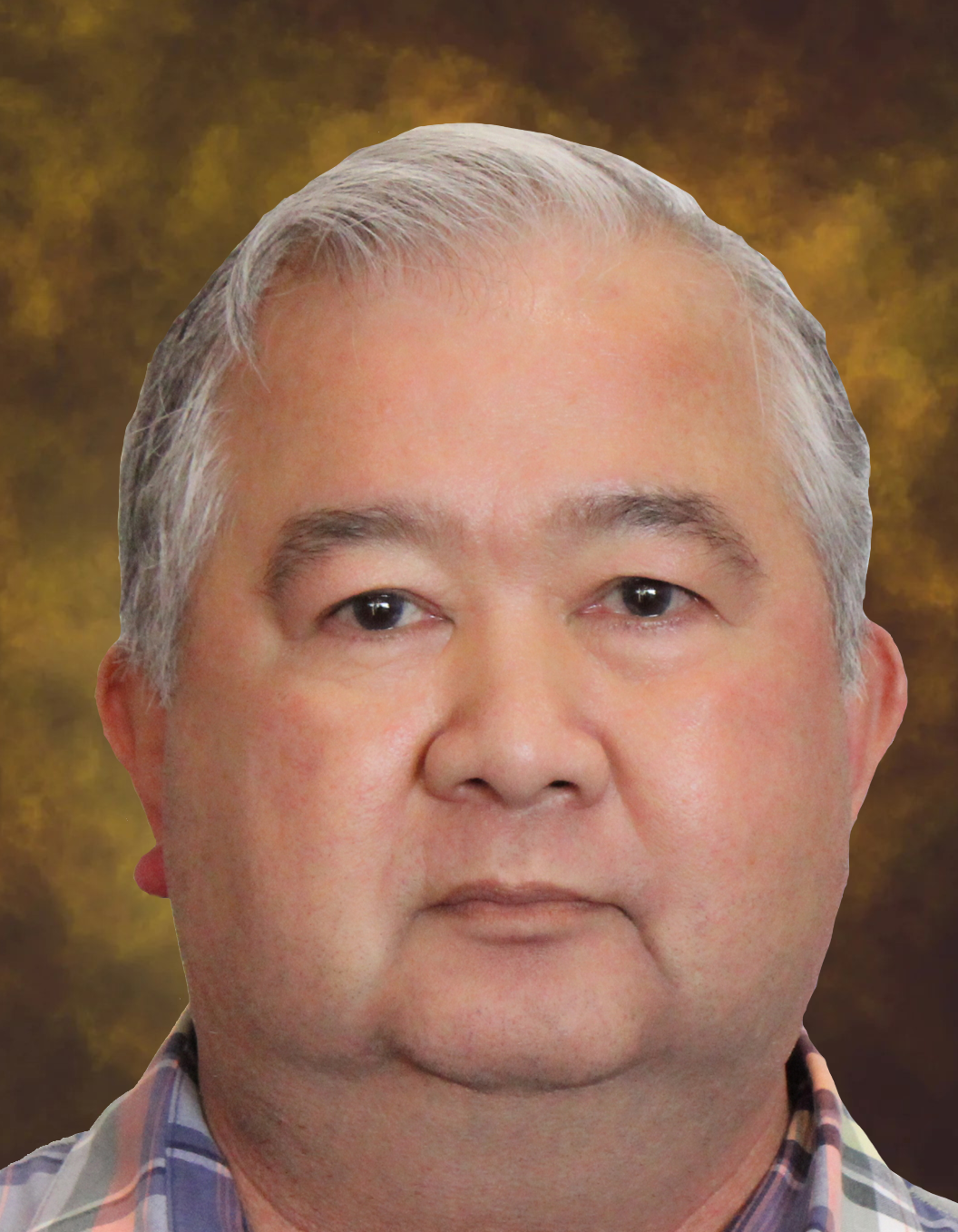
Photo taken
31 March 2025
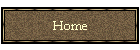
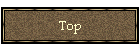
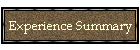
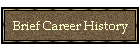
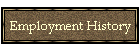
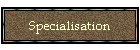
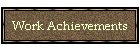
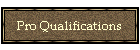
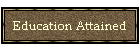
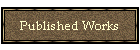
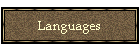
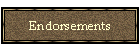
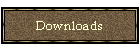
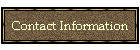
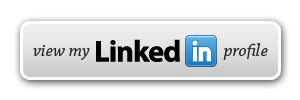
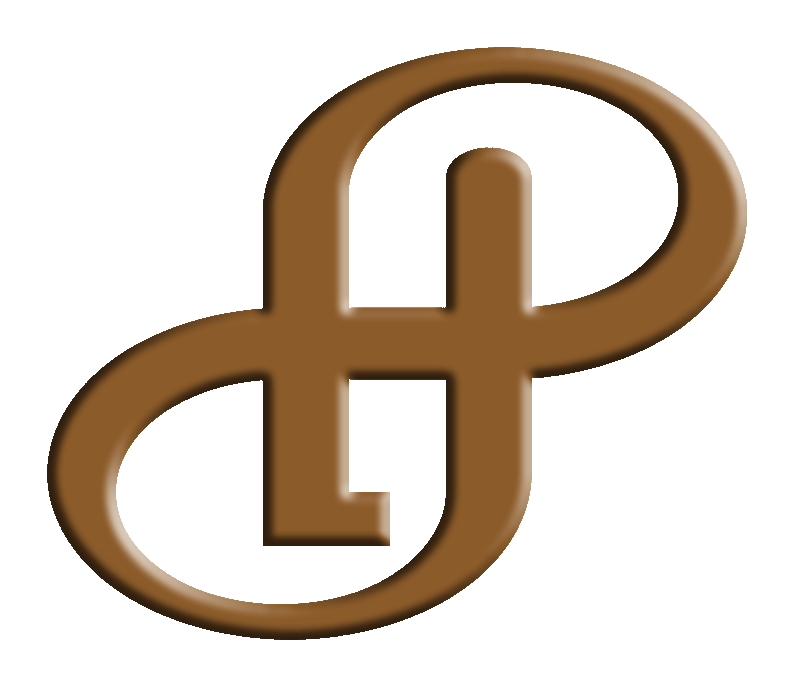
| |
PAST DUTIES AND
RESPONSIBILITIES
Position Name
|
QUALITY REPRESENTATIVE |
Position Location
|
Personalisation Plant - Highett |
Purpose
|
Maintenance and continuous improvement of the PN Plant’s ISO9002
management system within the corporate framework and to provide
leadership/guidance on quality matters to site personnel |
Scope
|
Personalisation Plant - Highett |
Reporting Relationships
|
DIRECT REPORT TO:
 | Plant Manager |
DIRECT REPORTS:
 |
Nil |
REGULAR LIAISON WITH:
 |
Shift Managers; SDL & Development Manager; Process Improvement Engineer;
Maintenance Supervisor; Operators; customers and suppliers; third party
certification bodies
|
|
What the incumbent needs to bring to the position
|
 |
1-2 years experience in Quality Management/Assurance/Control |
 |
Experience in quality management/ process improvement including
implementing quality management systems and audits and using continuous
improvement tools and techniques. |
 |
Good understanding of ISO 9001:2000 |
 |
Excellent written and oral communication skills |
 |
Proven ability to apply an analytical approach to investigations and
utilise problem solving skills to develop effective solutions |
 |
Ability to co-ordinate, implement and manage projects and process
improvement |
 |
Able to develop and document standards; test methods and write
procedures |
 |
OHS Awareness |
 |
Customer Focus (Internal and External) |
 | Intermediate computer skills |
|
Key Activities and Responsibilities
|
SAFETY
 |
Monitor
and ensure compliance to OH & S policies and procedures to help provide
a safe working environment |
 |
Actively participate in hazard identification and resolution at the
local level |
COMMUNICATION
 |
Collect and analyse process
and product data to identify improvements and report results to the PN
Plant Manager, Process Improvement and manufacturing teams. Ensure
standards are published, maintained and improved. |
 |
Provide regular reports on
Personalisation KPI’s or as directed by the PN Plant Manager. |
 |
Ensure that identified
records are maintained and retained for the Personalisation area in
accordance with written procedures. |
 |
Provide a monthly report
detailing key activities undertaken, results, analysis of NCR’s,
complaints corrective actions, audits and other performance needs as
linked to the KPI’s for national distribution. |
 | Liaise with certification bodies and customers
to facilitate assessments of the PN area to ISO9001:2000 and other
standards as appropriate. |
QUALITY
 |
Ensure
that process controls are developed, implemented, documented. |
 |
Maintain master files for Procedures, Manuals, Forms and provide master
lists for control purposes, in accordance with documented procedures. |
 |
In
conjunction with Team Leaders and Shift Managers, investigate and
identify the root causes of customer complaints, determine remedial
actions, assist with implementation and conduct any final rectifications
required in accordance with documented procedures. |
 |
Ensure
that data collection systems are developed and maintained to acquire
data for nominated Key Performance Indicators (KPI’s). |
 |
Conduct
and document Management Review Process |
 |
Ensure
that procedures are developed and documented to an approved format and
implemented for all PN plant activities. |
 |
Monitor
the conduct of process inspections, tests and audits to ensure they are
carried out in accordance with documented procedures and manufacturing
instructions |
 |
Ensure
that appropriate quality standards are developed, documented and
maintained for product control |
 |
Assist
Team Leaders to carry out identified corrective actions in accordance
with documented procedures |
 | Conduct internal audits
within the PN area in accordance with written procedures |
HOUSEKEEPING
 |
Monitor that the work area is kept clean and tidy and take corrective
action where appropriate |
SECURITY
 |
Ensure that Leigh-Mardon’s security procedures (both IT and physical)
are followed and consult with supervisor / manager before taking
correction |
TRAINING
 |
Assist
the PN Plant Manager to develop direct reports by highlighting and
identifying training needs |
VALUE CREATION
 |
Participate in continuous quality improvement to ensure organisational
effectiveness |
 |
Provide
innovative solutions to issues management in production environment |
 |
Offer
ideas to create value for the company and its customers |
 |
Encourage team members to offer ideas |
 | Identify items of
potential value to customers and devise means by which the manufacturing
plant can contribute toward their implementation |
ETHICAL STANDARDS
 |
Monitor
that Leigh-Mardon’s ethical behaviour standards are observed by self and
fellow team members and consult with supervisor / manager before taking
corrective action |
OPERATIONAL
 |
Assist with
the development of systems to meeting ISO90001:2000 certification and
maintenance thereof. |
 |
Participate in quality improvement activities |
 |
Monitor
Team Leaders conformance to written procedures regarding handling
non-conforming material and communications with suppliers for externally
sourced products. |
 |
Audit
registers and files for all non-conformance, situations in
Personalisation. |
 | Ensure that the product
audit system is carried out by the Production Teams. |
SCHEDULING AND PLANNING
 |
Develop and
provide input into the PN budget |
 | Maintain
internal and external audit schedules. |
|
Delegations / Authorities
|
Authorising Purchasing Requisitions for services and supplies to maintain
daily operations of the PN QA function up to $1,000.00 |
|
|
|